Skyline Cone Mill
The cone mill is also called the conical screen mill. One of its distinguishable features is a cone-shaped chamber fitted with a rotary impeller/knife.
Materials are fed into the cone mill in several ways:
- Hand feeding
- Vacuum feeding
- Gravity feeding
Cone mills are highly flexible and widely used for intermediate sizing in wet and dry granulation processes.
Working Principles
>> Materials are fed into the conical mill chamber through the in-feed chute. Feeding can be through gravity where an IBC bin/drum is interlocked onto the cone mill and inverted. When the butterfly valve is open, the Power particles flow into the conical mill.
>> As the Power particles come into contact with the rotating impeller, they are broken up through shearing & attrition and flung against the perforated sieve .
>> Desired grain sizes pass through the screen’s holes.
>> Increasing the speed of the impeller can result in smaller granules since it flattens the approach angle of particles to the screen’s surface.
>> Processed Power particles are collected in the receptacle, or vacuum conveyed to the next process equipment.
Cone mills can utilize different screen types. And what distinguishes them is the shape of the holes:
Round hole sievesMost conical mills utilize round hole sieves. You can use them with most free-flowing materials including granules & powders, it depends on your process requirements.
Square holes
Square hole screens produce coarse particles. They are applied in de-lumping & de-agglomeration wet masses.
Grater holes
Consists of holes that have been raised to create sharp cutting edges. Grater sieves can break down hard substances for instance tables during reprocessing and reworking operations. In food industries, grater sieves can grate sweets, tough seeds, etc.
Conider hole
Conider sieves consist of a sheet with raised holes that are triangular-shaped or semi-oval.
Features
- Uses Centrifugal force for both Milling and Sifting
- Gentle grinding action with close particle size distribution
- Minimal fines generation
- Charging of material- either gravity fed or vacuum transferred
- Increased throughput with 50% more capacity than conventional mills
- Adaptable & flexible design with interchangeable Cone mill and Rotary sifter and through the wall design
- Customised options for feeding and handling
- Readily available scale up from lab to production scale
- Material of construction : SS 316 / SS 316L / Food grade materials
- Easy to clean
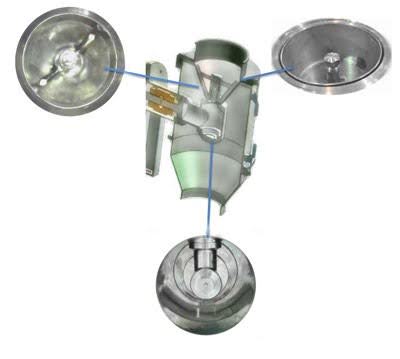